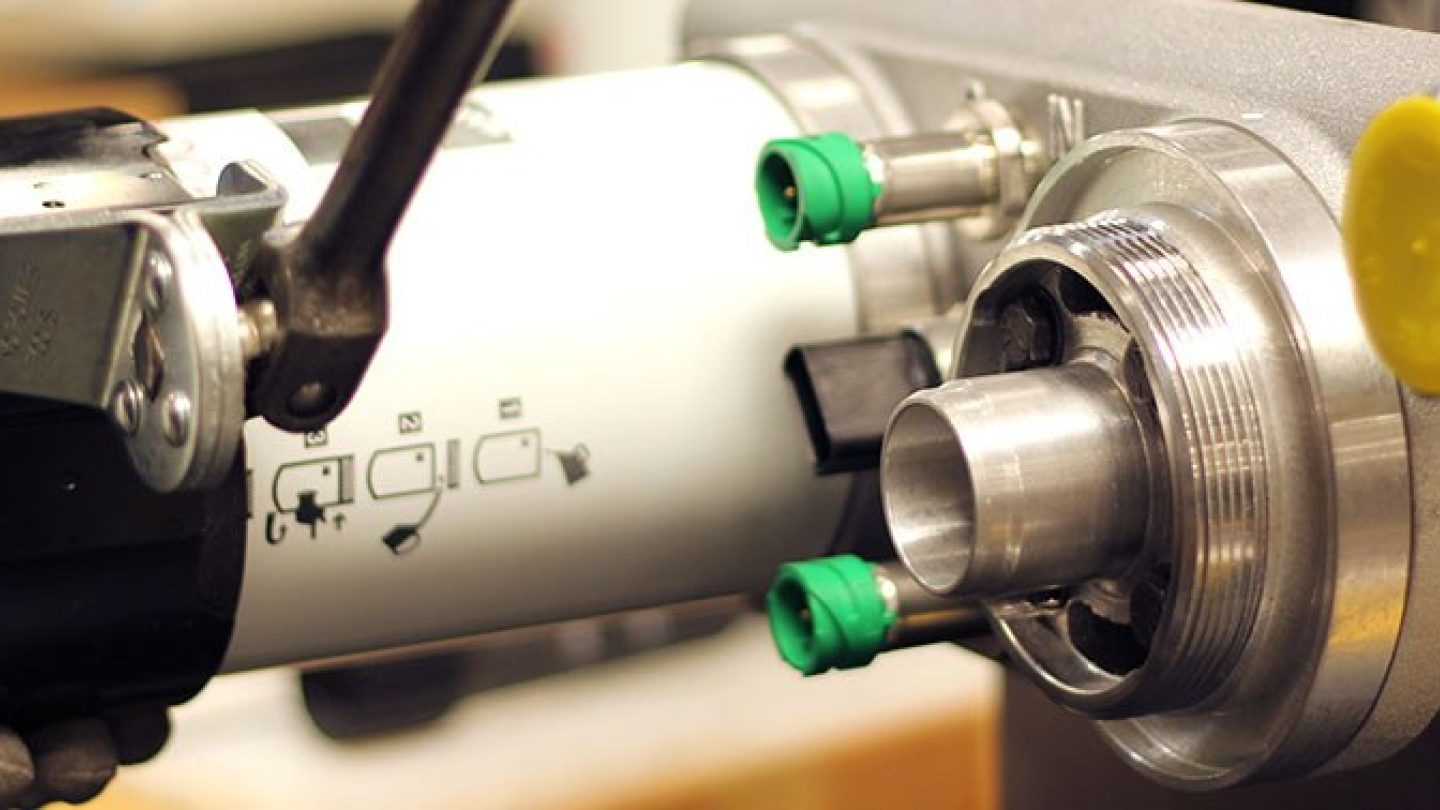
Parts Inspection Services
Elevating Manufacturing Quality & Integrity
Parts inspection services refer to the comprehensive assessment and evaluation of various components, parts, or products within the manufacturing industry. Inspection services involve a systematic examination to ensure that the manufactured parts meet the required specifications and quality standards. This essential process plays a pivotal role in maintaining product integrity, minimizing defects, and ensuring customer satisfaction.
In the realm of manufacturing, inspection is an indispensable aspect that safeguards the overall quality of the end product. Parts inspection serves as a critical quality control measure, acting as a checkpoint throughout the manufacturing cycle. By conducting thorough inspections, manufacturers can identify and rectify any deviations or discrepancies early on, preventing costly production delays and potential safety hazards.
The inspection process in manufacturing typically involves various stages, starting from incoming raw materials and components, progressing through intermediate stages, and culminating in the final product. Skilled inspectors employ a range of techniques, including:
Visual examination
Dimensional measurements
Material tests
Functional tests
Non-destructive testing methods
Inspectors use techniques like these to assess the quality, dimensional accuracy, performance, and structural integrity of parts.
The importance of parts inspection services is extremely high. Firstly, effective and efficient part inspection helps ensure that the components used in the manufacturing process meet the required specifications and are free from defects. This, in turn, enhances the overall reliability and functionality of the final product. Secondly, parts inspection services help ensure that products adhere to industry standards and governmental regulations.
Inspection services also play a pivotal role in maintaining customer satisfaction. By meticulously inspecting parts, manufacturers can identify and address potential issues before the products reach the market. This not only helps in reducing customer complaints but also builds a reputation for delivering high-quality and reliable products.
A Closer Look at the Inspection of Machined Parts
Inspection of machined parts is a crucial process within the manufacturing industry. Diligent inspection ensures the quality, precision, and reliability of essential manufacturing components. Machined parts inspection services encompass a range of techniques designed to thoroughly evaluate the characteristics and performance of these parts.
The Essential Role of Visual Inspection
Visual inspection serves as a fundamental method in machined parts inspection services during which trained inspectors carefully examine parts to identify any visible defects, surface irregularities, or anomalies. This form of inspection relies on the expertise of inspectors to detect imperfections that may impact the overall quality or functionality of the part.
The Precision and Importance of Dimensional Inspection
Dimensional inspection focuses on verifying that machined parts conform to the specified dimensional tolerances. Precision measurement tools, such as calipers, micrometers, and coordinate measuring machines (CMMs), are typically utilized to assess the geometries of the parts. By conducting dimensional inspections, manufacturers ensure that their parts fit precisely and function effectively within their intended applications.
Why Material Testing is Crucial
Material testing is another crucial aspect of machined parts inspection. Material testing involves analyzing the composition and properties of the materials used in the parts. Material testing factors may include:
- Hardness
- Tensile strength
- Chemical composition
- Metallurgical properties
Testing these factors can help manufacturers verify that their parts are made from appropriate materials and possess the necessary mechanical characteristics for their intended purposes.
The Value of Non-Destructive Testing
Non-destructive testing (NDT) techniques assess the integrity of machined parts without causing damage. Methods such as ultrasonic testing, magnetic particle inspection, and liquid penetrant testing can be useful for identifying internal defects, cracks, or flaws that may not be visible to the naked eye. NDT plays a critical role in ensuring the structural soundness and reliability of parts.
The Role of Functional Testing in Quality Assurance
Functional testing involves subjecting machined parts to simulated operating conditions to evaluate their performance. Functional testing may involve applying loads, pressures, or temperatures to assess whether the parts meet required performance standards. Functional testing is essential for verifying that all parts perform as intended in real-world applications.
Rigorous Examination: The Art and Science of Small Part Inspection
Small part inspection is the meticulous process of assessing and evaluating small-sized components to guarantee their quality and dependability. Small parts can be found in various industries, including automotive, aerospace, medical devices, and electronics.
In industries like these, small parts play crucial roles in the overall functionality and safety of final products. Due to their miniature size, small parts demand particular attention during the inspection process to ensure they meet the required specifications.
The value of small part inspection should not be underestimated. Even the slightest variation in size, shape, or material composition can have a significant impact on the performance and reliability of the end product. A flaw in a component such as an electronic connector or a medical implant could lead to malfunctions that compromise patient safety. It’s absolutely critical for small parts to undergo thorough inspection procedures so any defects or deviations can be identified and rectified early on.
The process of small part inspection involves a combination of visual examination and precision measurement techniques. Skilled inspectors use magnification devices, such as microscopes and magnifying lenses, to thoroughly examine the parts for surface defects, imperfections, or anomalies. Precision measurement tools like micrometers, calipers, and optical comparators are often employed to assess the dimensional accuracy and tolerances of small parts.
In some cases, specialized inspection techniques may be required for small part inspection. For instance, non-destructive testing methods, such as X-ray imaging or ultrasonic testing, are sometimes used to detect internal defects or structural irregularities that may not be apparent during a visual inspection.
By subjecting miniature components to rigorous inspection procedures, manufacturers in numerous industries can identify and address issues that may compromise the performance, safety, or longevity of their final products.
The Role of Quality Assurance for Machined Parts
Quality assurance for machined parts is a crucial aspect of the manufacturing process. Quality assurance aims to guarantee that all machined parts meet the required quality standards. By implementing effective quality assurance measures and utilizing parts inspection services, manufacturers can:
Ensure product quality
Reduce costs
Mitigate risks
Comply with industry standards and regulations
Spare parts quality assurance begins with thorough part inspection. Part inspection services perform comprehensive assessments of the machined parts, including examinations of their dimensions, tolerances, materials, and overall quality. By using techniques like visual inspections, dimensional measurements, material testing, non-destructive testing, and functional testing, parts inspection services help manufacturers identify parts defects that may affect the performance or safety of the products they produce.
Benefits of Parts Inspection Services
One of the primary benefits of parts inspection services is ensuring product quality. By carefully inspecting machined parts, manufacturers can address problems before they impact the production process or customer satisfaction.
Additionally, parts inspection services can lead to cost reductions. By locating and fixing defects early on in the manufacturing process, manufacturers can avoid production delays or customer returns. Effective quality assurance also helps manufacturers optimize their production processes and improve overall efficiency, leading to more cost savings in the long run.
Another advantage of quality assurance for machined parts is risk mitigation. Thorough inspections help identify potential risks like structural weaknesses. By addressing these risks during the inspection process, manufacturers can prevent serious product failures that lead to safety hazards and liability issues.
Furthermore, quality assurance helps manufacturers maintain compliance with industry regulations. Each industry has specific quality standards and regulatory requirements that manufacturers must meet. By implementing parts inspection services, manufacturers can demonstrate their commitment to producing safe and compliant products.
Striving for Perfection: Emphasizing Zero Defect in Quality Management
“Zero defect” in quality management refers to the philosophy of striving for flawless performance and eliminating defects throughout the manufacturing process. A zero defect approach ensures that every product or component meets the required quality standards, leaving no room for errors.
Zero Defect Manufacturing in the Aerospace Industry
In the aerospace industry, zero defect manufacturing is of paramount importance due to the stringent safety requirements and high-stakes nature of the industry. Any defect in aircraft components can have catastrophic consequences, which means rigorous parts inspection services are necessary to ensure the integrity and reliability of aerospace parts.
The Role of Zero Defect Manufacturing in the Automotive Industry
The automotive industry also places significant emphasis on zero defect manufacturing. As vehicles become increasingly complex, the need for flawless components is essential to maintain high levels of performance and safety. Parts inspection services help automotive manufacturers verify the dimensional accuracy, material integrity, and functional performance of automotive parts.
The Essentiality of Zero Defect Manufacturing in the Manufacturing Sector
In the manufacturing sector, zero defect manufacturing is vital for maintaining high-quality standards and minimizing waste and rework. Parts inspection services play a crucial role in detecting and rectifying defects early in the production process, ensuring that only defect-free components proceed to the next stages of manufacturing.
Zero Defect Manufacturing in the Medical Devices Industry
The medical devices industry requires zero defect manufacturing to ensure the safety and effectiveness of devices used for patient care. Parts inspection services help verify the precision and compliance of medical device components, lowering the risk of device failures.
There are numerous benefits to implementing zero defect manufacturing, including:
Ensure customer satisfaction
Reduce costs associated with rework or product failures
Enhance brand reputation
Improve overall process efficiency
By implementing parts inspection services and adhering to rigorous quality control measures, manufacturers in various industries can minimize defects and achieve the highest possible levels of product reliability.