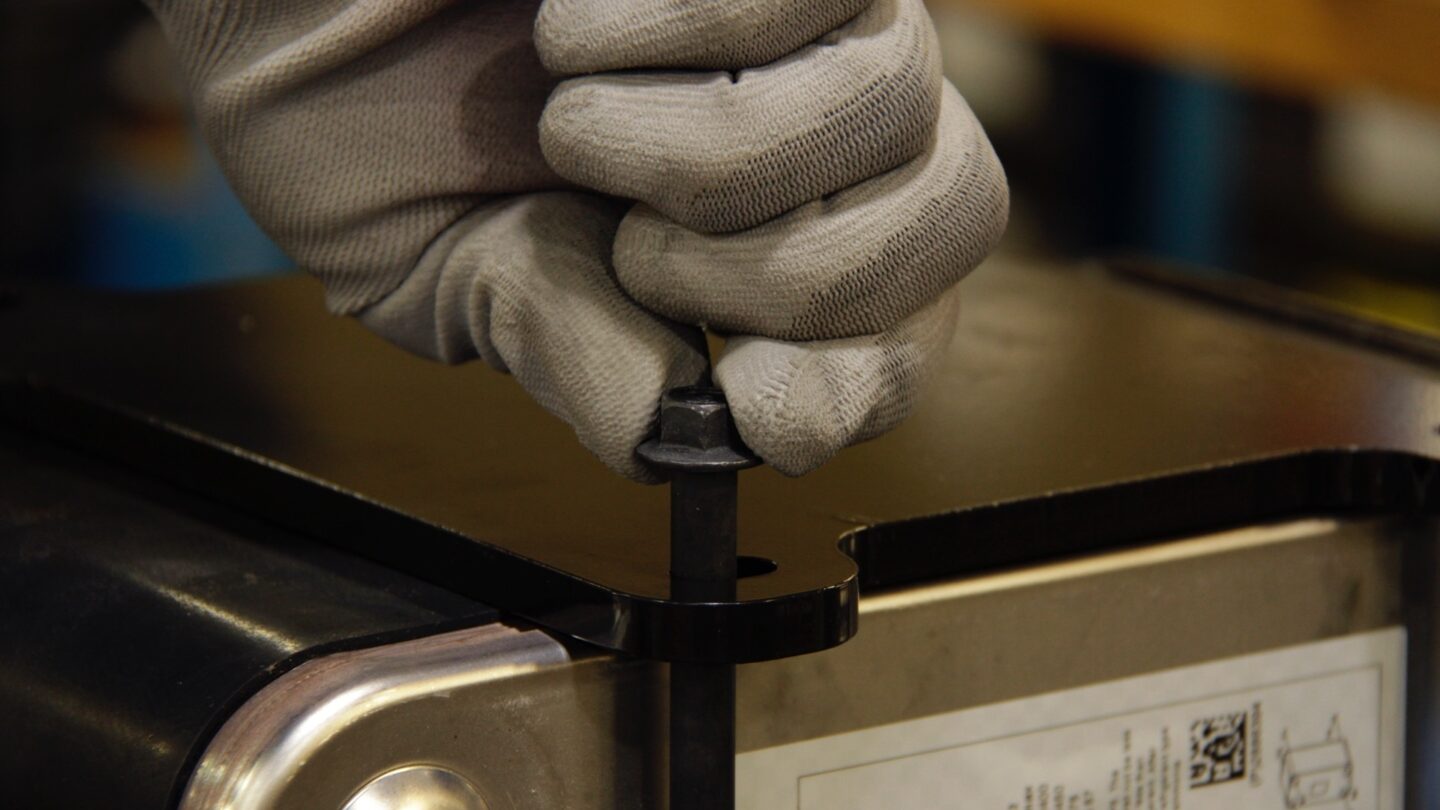
Assembly vs. Sub-Assembly
Unraveling Manufacturing Processes
Assembly and sub assembly are two fundamental processes in manufacturing that allow for complex product creation. They involve combining multiple individual components to create items. Understanding assembly vs. sub assembly is critical to understanding the supply and production chain as a whole, as both contribute to the efficient and systematic production of goods.
Assembly is a broad term used to describe the process of combining individual components to create a functional product. This process often involves the use of techniques such as welding, gluing, riveting, or fastening. The final result of an assembly process could be any fully formed product, like a car or computer.
Sub-assembly is a smaller-scale process in which individual components are put together to form a larger part that will eventually be used in the assembly of the final product. A sub-assembly is an assembled unit or an intermediate assembly that is part of a larger assembly.
These processes can be clearly illustrated in car manufacturing. The engine is a complex machine consisting of numerous smaller parts like pistons, crankshafts, and spark plugs. Each of these parts is assembled together to create the engine, which is then used in the car's final assembly.
The difference between sub assembly vs. assembly can likewise be seen in making a computer. For the sub assembly process, the motherboard, which consists of smaller components like the CPU and input/output controllers, is put together. The larger assembly might involve integrating the motherboard, hard drive, and other parts to create the computer.
Ultimately, the key distinction between these processes lies in the level of the process within the overall production chain. An assembly process leads to the creation of a final product, while a sub-assembly process leads to the creation of an intermediary product that will eventually be used in the assembly process.
Strategically leveraging these processes can result in many benefits for a production line. Breaking down a complex product into smaller sub-assemblies allows for specialization and efficiency in production. Each sub-assembly can be created independently, potentially at different locations or times, and brought together during the final assembly. This can improve production efficiency and allow for easier quality control.
Understanding Assembly
The role of assembly in manufacturing is critical, as it joins all parts to create a functional product. Many people believe that items come together in a single, uniform process, but this couldn’t be further from the truth. In reality, the assembly process in manufacturing very often involves multiple steps and sub-components.
It begins with the sourcing of individual parts, which may be produced in-house or supplied by other manufacturers. These components are then assembled based on a plan or blueprint outlining the steps necessary to construct the finished product. This plan serves as a crucial guide for workers or automated machinery that carry out the assembly process.
The assembly process can range from simple to complex, depending on the product being produced. In the case of a relatively simple product, such as a ballpoint pen, the assembly might involve only a few components and a simple procedure. An automobile, on the other hand, requires a multi-step assembly process and sub-assemblies.
For example, smaller components might be assembled into sub-assemblies like the engine, transmission system, or dashboard when producing a car. These sub-assemblies are then combined in the final stage of the assembly process to create the finished car.
Understanding assembly and the various benefits it offers can make for a more efficient manufacturing process all around. Advantages of assembly include:
Economies of Scale: When products are assembled in large volumes, the cost per unit decreases, making products more affordable for consumers.
Production of Complex Products: Assembly allows for the creating of complex products composed of multiple parts.
Customization: By adjusting the assembly process or using different components, manufacturers can create various product versions to meet diverse customer needs.
Efficient Use of Resources: Assembly processes can optimize labor and material usage, increasing productivity and reducing waste.
Still, the assembly process is not without its challenges. When assembling products, it’s important to consider:
Quality Control: With numerous components being combined, the risk of defects or malfunctions increases. Rigorous testing and quality checks are necessary but can add to the cost and time of the assembly process.
Complexity: Managing the sequence of assembly operations, coordinating logistics of parts supply, and orchestrating human or machine labor can be complicated and demanding.
Dependency on Suppliers: If components are sourced from external suppliers, any disruptions in supply can directly impact the assembly process.
Despite these challenges, assembly remains a fundamental aspect of manufacturing. Its end result is a product that offers more value than the sum of its individual components. During this stage, the functionality and reliability of the product are tested, ensuring safety and quality.
Understanding Sub Assembly
In the manufacturing sector, the sub assembly process represents a smaller step in the broader assembly process. Understanding sub-assembly can be difficult for those new to the process, but it is important to boost efficiency.
So what is sub assembly manufacturing? Sub-assembly is the point in the production process where sub-assemblies or modules are used to construct the final product. These sub-assemblies are often produced independently of the final assembly, sometimes even at different locations or by different companies, and then brought together for the final assembly process.
Viewing sub assembly examples can be a good way to learn more about this process. One example in which the importance of sub-assembly is clearly seen is car manufacturing. Here, sub-assemblies may include the engine, transmission, or dashboard. Each component is built separately, with numerous parts being joined together to create the sub-assembly.
It’s easy to see why the role of sub-assembly in manufacturing is so important. It allows manufacturers to enact better quality control measures, as they can assess each part individually instead of simply looking at the finished product as a whole. Here’s a closer look at some of the key benefits of sub-assembly:
Efficiency: The manufacturing process can be more easily streamlined when complex products are broken down into smaller sub-assemblies. This can result in shorter production times and lower costs.
Quality Control: Creating sub-assemblies is a great way to conduct quality checks at each stage of the manufacturing process. This makes identifying and rectifying issues easier before they become even bigger problems.
Specialization: The sub assembly manufacturing process allows for parts of the production process to be outsourced to specialists. This can lead to higher quality sub-assemblies and a more efficient overall production process.
Like the larger assembly process, however, sub-assembly can be challenging for several reasons, such as:
Logistics and Coordination: Managing the logistics of producing and transporting sub-assemblies can be challenging. Careful coordination is needed to ensure all sub-assemblies are produced on time and in the correct order.
Dependency on Suppliers: If sub-assemblies are outsourced, suppliers' delays or quality issues can directly impact the final assembly process.
Inventory Management: As sub-assemblies are often produced before the final assembly, managing inventory can be challenging. Overproduction can lead to unnecessary storage costs, while underproduction can delay the final assembly.
Choosing Between Assembly and Sub Assembly
Choosing between assembly and sub-assembly should be a strategic decision that’s considered from all angles. A full assembly process may suffice when dealing with simple products consisting of few components. These products can be assembled from start to finish in a single, straightforward process.
In a small toy manufacturing unit, a rubber duck toy might consist of only a few parts—the body, the head, and the squeaker. These components can be assembled in one process, making the sub-assembly procedure unnecessary.
More complex products with numerous individual parts will likely require some sub-assembly to streamline production and improve quality control. Take, for example, a large automotive company. Cars are highly complex products that consist of thousands of individual parts. Trying to assemble such a product in a single step would be inefficient and prone to errors. Instead, these companies often utilize a sub-assembly process.
In this context, sub-assemblies like the engine and transmission system are created separately, each being a significant process. The engine sub-assembly might occur in one factory section, while the interior furnishings might be assembled elsewhere. These sub-assemblies are then brought together in the final assembly process to produce the completed car.
The decision between an assembly or sub-assembly process often comes down to a company's specific capabilities and resources. An organization with a high degree of specialization in a particular area might focus on producing a specific sub-assembly, which it can then supply to other manufacturers. For instance, a company specializing in electronic components might produce circuit boards (a sub-assembly) that other companies use in their final assembly processes.
The importance of assembly and sub-assembly cannot be overstated, which is why many businesses go to great lengths to put the proper tools and processes in place to ensure smooth production. MSW offers quality assembly and sub-assembly solutions to mitigate risk and get the ball rolling on production as quickly as possible. This is key to a successful overall production process.