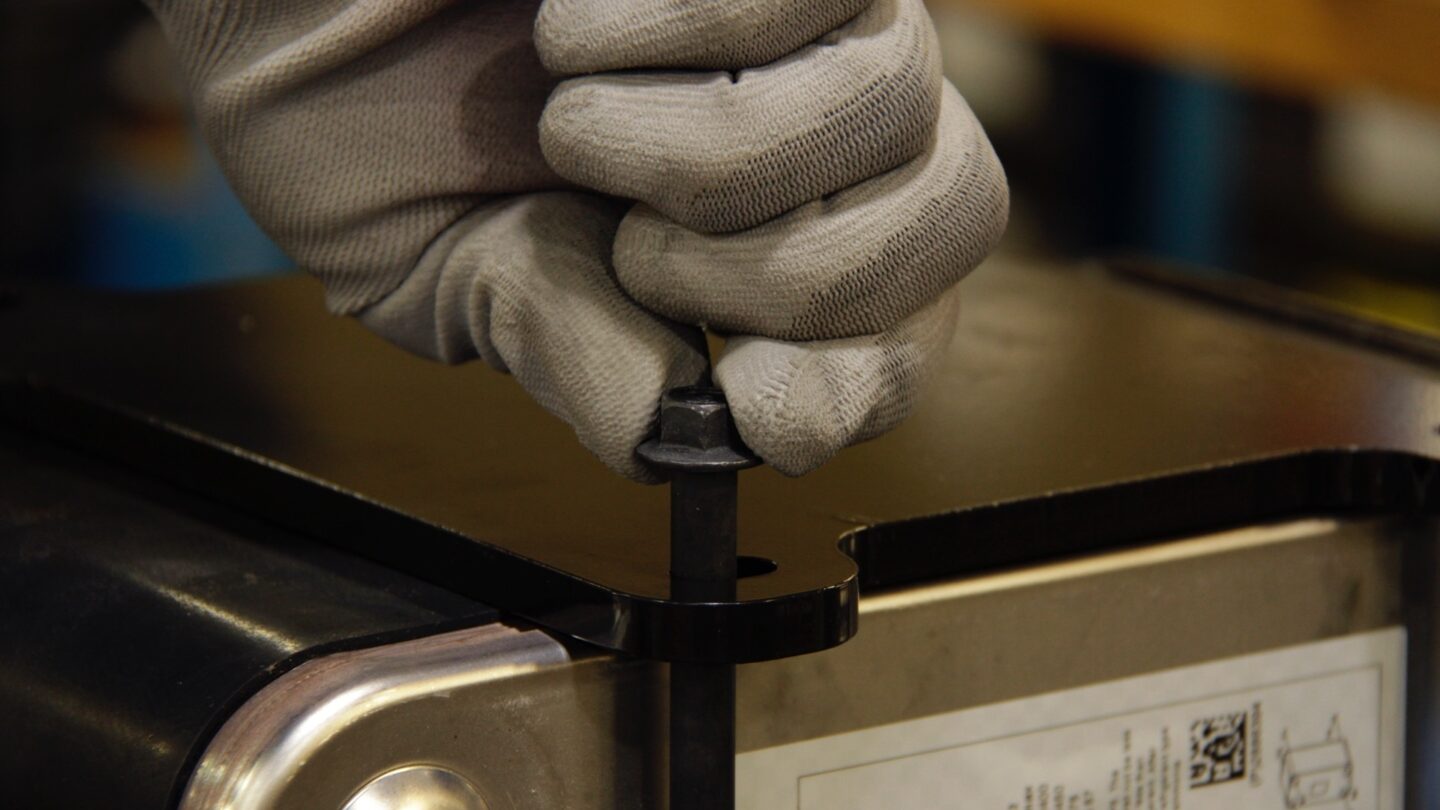
A Deep Dive into Aerospace Assembly
Aerospace assembly refers to the process of constructing and integrating various components of aircraft, spacecraft, and other flight systems. This complex procedure involves the synchronization of numerous parts and technologies. The assembly process necessitates great precision, as even the smallest errors can lead to disastrous consequences.
There are many different types of assembly in aerospace. One is structural assembly, which involves the construction and assembly of the main body of an aircraft or spacecraft. This includes the fuselage, wings, tail sections, and other structural components. Another is systems assembly, which deals with the integration of subsystems like avionics and propulsion systems.
The aerospace industry continuously innovates to improve its assembly processes. Modern aerospace assembly solutions utilize advanced technologies to enhance safety and efficiency. For instance, automated drilling and fastening systems are used to minimize errors and speed up assembly times. Similarly, robotic arms are utilized to handle large and heavy components.
The Aerospace Assembly Process
The utmost precision in aerospace assembly is vital, and every step of the assembly process is subjected to stringent aerospace quality control measures. The following are the key stages of the aerospace assembly process:
Design and Planning: Before the physical assembly begins, engineers and designers create detailed plans and models of the aircraft or spacecraft, including all the intricate systems and subsystems. These designs establish that all aerospace components meet specific design specifications. At this stage, quality control involves rigorous scrutiny of the designs to eliminate any potential design flaws.
Fabrication of Components: This stage involves the manufacturing of individual aerospace components such as bolts, screws, wing sections, engine parts, fuselage components, landing gears, and more. The fabrication must adhere to strict tolerances due to the demanding environment these components will operate in. Quality control at this stage requires thorough inspection of each part for any deviations from the specified dimensions or any material flaws.
Structural Assembly: The individual components are brought together to form larger structural elements. Quality control measures at this stage include structural inspections and tests to ensure accurate alignment and proper fit of the components.
System Integration: In this phase, systems are integrated into the structure. These systems are critical for the operation of the aircraft or spacecraft. Here, quality control procedures include rigorous testing of all systems under simulated operational conditions to provide greater functionality and reliability.
Final Assembly: All the assembled parts and systems come together in the final assembly. The aircraft or spacecraft begins to take its final form at this stage. A series of inspections and tests are performed to verify the correct installation and integration of all systems.
Painting and Finishing: The exterior of the aircraft or spacecraft is painted and furnished. Although this might seem aesthetic, the paint job can affect the aircraft's weight and aerodynamics. The uniformity and quality of the paint job are checked to make sure they adhere to all relevant standards.
Testing and Certification: The final stage in the aerospace assembly process is comprehensive testing. The aircraft or spacecraft undergoes a series of ground and flight tests to verify its performance and safety. Aerospace quality control at this stage is critical to make the aircraft or spacecraft safe for operation. Any issues identified during testing are rectified before the final certification is granted.
Following this process carefully is paramount to the safety, functionality, and performance of aircraft and spacecraft. Every step of this process is meticulously designed and executed to make sure that all parts and systems fit together precisely and operate as intended.
MSW’s assembly services come with the type of stringent quality control measures demanded in aerospace. By working with MSW, businesses can ensure all components are functioning correctly and up to par with industry standards.
Challenges in Aerospace Assembly
Industry professionals face several challenges in aerospace assembly today. These issues range from the production of individual components to the integration of complex systems and subsystems.
One of the major aerospace quality challenges encountered during assembly is maintaining high levels of accuracy. All components must fit together with extreme accuracy. A minor misalignment or improperly fitted part can negatively impact the entire aircraft or spacecraft's performance and safety.
To address this, strict quality control measures are implemented at every stage of assembly. Such measures include rigorous inspections, testing under simulated conditions, and the use of advanced technologies such as automation and digital twin technology to enhance precision and detect potential issues early.
Material selection also presents unique challenges in aerospace assembly. Aerospace components must be able to withstand extreme conditions, including high pressures, temperatures, and forces. Materials used in aerospace should thus possess specific properties such as high strength-to-weight ratios and thermal stability.
However, working with these advanced materials can be challenging and requires specialized skills and equipment. To tackle this problem, aerospace manufacturers typically invest in continuous workforce training and the latest manufacturing technologies.
Aerospace regulatory standards also shape the aerospace assembly process and present their own set of challenges. Regulatory bodies such as the Federal Aviation Administration (FAA) in the United States and the European Aviation Safety Agency (EASA) in Europe impose rigid standards to promote the safety and reliability of aerospace vehicles.
These standards dictate everything from the design and manufacturing of aerospace components to assembly processes and testing procedures. Compliance with these standards can be challenging, but it’s essential to avoid legal implications. For this reason, regulatory standards are often incorporated into the assembly process from the earliest stages.
Innovations in Aerospace Assembly
Innovations in aerospace assembly are being introduced on a regular basis. Two of the most significant advancements revolutionizing this field are aerospace automation and the use of artificial intelligence (AI), both of which are rapidly changing the way assembly is done.
Aerospace automation is a process that leverages automated machinery and robotics to execute tasks traditionally performed by human operators. This technology has a transformative impact on the aerospace assembly process, leading to significant improvements in production speed, precision, and repeatability. For example, automated drilling and fastening systems are now commonly used to assemble large structural components.
Automation also reduces physical strain on human workers, particularly when handling large and heavy components. Robotic arms are used for lifting and positioning these parts, minimizing manual handling and the associated risks of injuries. Automated tools and systems can operate in hazardous environments or perform tasks that could be dangerous for human workers.
Another key innovation is the use of AI in aerospace assembly. One significant application is predictive maintenance, where AI algorithms analyze data from various sensors to predict potential component failures before they occur. This capability can significantly reduce unplanned downtime and associated costs.
AI can likewise be employed in quality control. Machine learning algorithms are capable of analyzing images or scans of assembled parts, detecting anomalies or defects that might be missed by human inspectors. This application not only enhances the accuracy of quality control, but speeds up the inspection process.
The use of AI extends to training as well. Virtual reality (VR) combined with AI can provide immersive training experiences for assembly line workers, helping them learn and practice assembly tasks in a safe, simulated environment. This approach can accelerate the learning process and prepare workers for the tasks they’ll perform on the actual assembly line.
The Future of Aerospace Assembly
When looking to the future of aerospace assembly, the spotlight is on new and innovative tools and techniques. The current aerospace industry outlook points to a growing focus on sustainability and efficiency, driving unlimited possibilities.
Here are some aerospace assembly industry trends to watch for today and in the near future:
Increased Automation and Robotics: Considering the notable benefits of automation in improving precision and safety, its adoption in aerospace assembly is expected to expand in the coming years. Robotic systems will likely become more sophisticated, handling more complex tasks with greater autonomy.
Wider Use of AI and Machine Learning: The application of AI in aerospace assembly is set to increase, with a greater focus on predictive maintenance, quality control, process optimization, and training. Machine learning algorithms will become more advanced and better able to analyze and learn from vast amounts of assembly data.
Advancement in Additive Manufacturing: Additive manufacturing, or 3D printing, holds great promise for the aerospace assembly industry. It allows for the production of lighter, stronger, and more complex components, and its use is likely to grow in the coming years.
Digital Twin Technology: The use of digital twin technology—creating a virtual model of a physical component or system—is expected to become more commonplace going forward. It allows for extensive testing and optimization in a virtual environment before physical assembly, saving valuable time and resources.
Sustainability Initiatives: Climate concerns are top of mind for many industries, and aerospace is no exception. This sector is increasingly prioritizing the development and assembly of more energy-efficient aircraft, the use of sustainable materials in assembly, and the implementation of greener assembly processes.
Workforce Training and Skills Development: As technologies evolve, there will be a greater emphasis on training and skills development to ensure the workforce can effectively leverage these new tools and techniques.
The evolution of the aerospace assembly industry aligns with the broader trend of digital transformation sweeping across various sectors. In the future, we can expect the aerospace assembly process to become even more sophisticated, driven by technological innovations, environmental considerations, and an emphasis on efficiency and safety.